This content was published: November 8, 2021. Phone numbers, email addresses, and other information may have changed.
Industry turns to PCC to help close the advanced manufacturing skills gap
Photos and Story by James Hill
Even before COVID-19, the field of advanced manufacturing was suffering a skills gap, meaning there weren’t enough qualified workers to fill specialized jobs within the sector. The arrival of a global pandemic certainly was another hit to industry; supply chains were disrupted, and the demand for certain goods plummeted.
The good news is that in spite of the ongoing pandemic, manufacturing jobs are making an impressive comeback. The bad news? The skills gap has widened, with those same jobs in even higher demand.
Oregon’s semiconductor manufacturing sector, considered the most automated industry in the state, is snatching up college graduate pools to fill the demand for workers. Hillsboro-based Jireh Semiconductor, Inc. has 60 openings currently and is in the middle of an expansion that could double this number by March 2022.
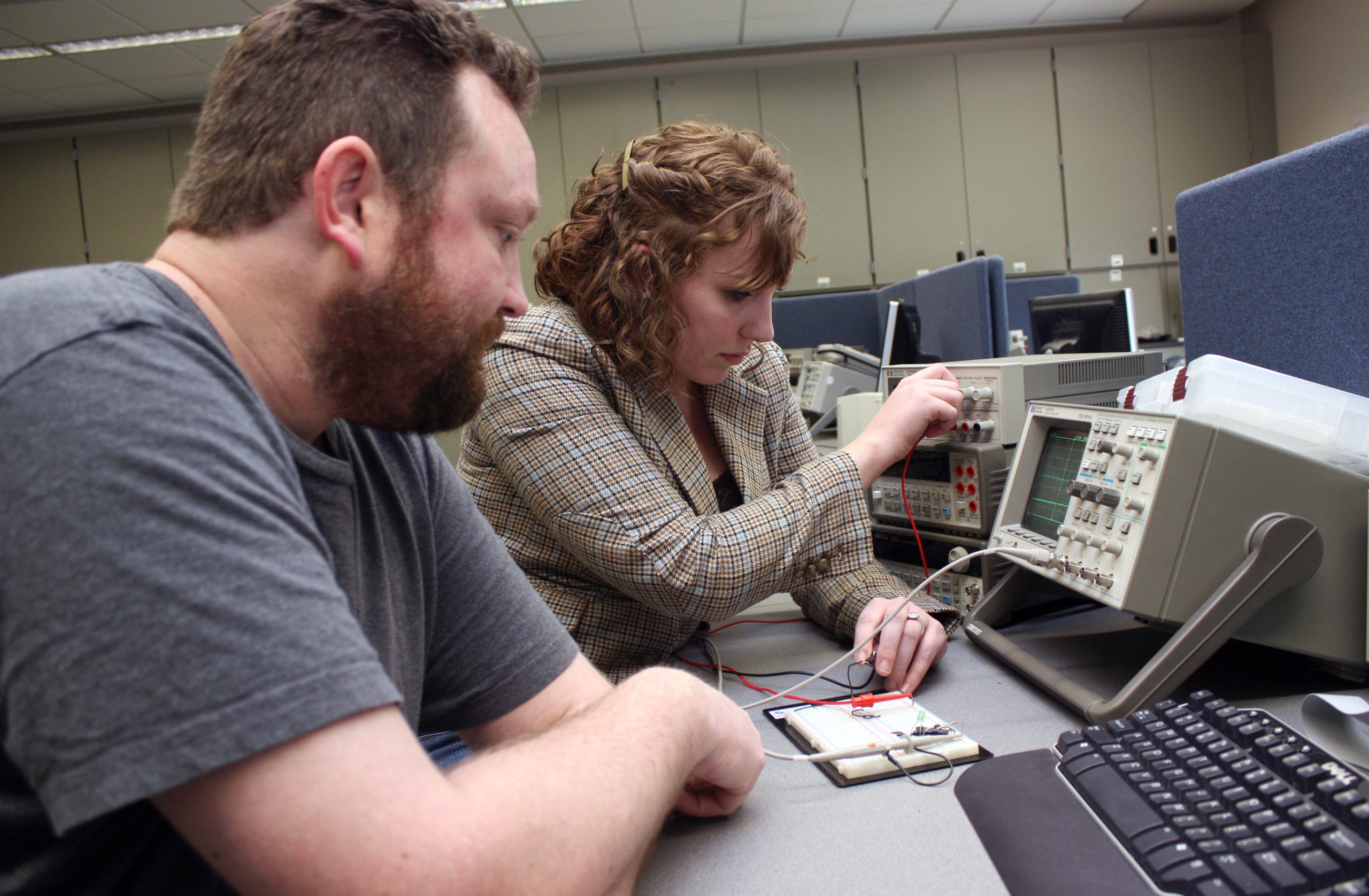
Microelectronics Technology Program
- The program has earned a reputation for excellence, specifically designed to meet the needs of industry.
- The college enjoys a strong partnership with local semiconductor manufacturers to provide qualified trained workers.
- Students can acquire skills that are in high demand while benefiting from PCC’s strong industry partnerships.
“Simply put, there are not enough employees for the number of jobs we have open,” said Lynn Nelson, Jireh’s HR and recruiting manager. “We are looking to find folks who are currently working toward degrees, and bring them in as part-time interns while they finish their studies. Within the industry, we are seeing unprecedented wages and bonuses being paid to current employees and candidates to attract any talent whatsoever. Companies also pay sign-on bonuses for entry-level positions with no experience.”
Industry need is prompting recruiters to knock on the doors of college training programs to find prospective graduates. Such programs are critical, said Nelson, to prepare students for high-tech positions; coursework teaches students how to fix and operate machinery, with some of the best employees being those who are in school as they can readily apply what they’re learning in class to their daily work activities.
“And students and graduates who have completed their coursework catch on much quicker, developing faster into these positions,” Nelson added.
Yet the numbers aren’t there; more students need to pursue this educational path to fill the industry gap — and to capture their interest, they need to learn about advancement opportunities in the field. To help with this, Jireh Semiconductor sits on Portland Community College’s Microelectronics Technology Program’s advisory board, which includes about 15 semiconductor companies. Members host mock interviews with students and mentor them, provide guest speakers and technical assistance to faculty, promote the program to their employees and friends, and donate equipment.
And, advisory board companies actively pursue the program’s students and graduates. For the past decade, between 90-100% of PCC students have been hired by these companies within three to six months of graduation.
Yet in the last four years, additional companies have expressed interest in hiring students as interns earlier in their pursuit of their microelectronics degree.
“Some are first-year students who have completed the first-term of the program, and some are students who have completed their first year,” said Bill Manley, PCC’s Jobs and Internships/Career Services Employment Specialist. “In light of the industry’s expansion, I expect these numbers to grow significantly in the future.”
Like Jireh, Lam Research has experienced unprecedented job growth over the last several years. Brian Clay, Lam’s Tualatin Operations Training Program Manager, explained that this was in part why the company developed an internship program with PCC. The internship launched in June 2020, during the pandemic, with a cohort of 12 students. This year’s cohort has 13 students.
“The potential candidate pool of qualified individuals has not been able to keep up,” Clay said. “We are constantly looking for candidates to fill open positions within manufacturing.”
Justin Stenberg began his internship at Lam Research in June 2020. He is working through PCC’s Microelectronics Technology Program and plans to graduate by the end of next spring. As an intern, Stenberg is learning the basics of being an assembler, putting together tool parts for the past six months.
“The internship has been a dream come true,” Stenberg said. “I knew I wanted to do something with my hands that involved new technology because I would have no problems finding a job.”
And it’s not uncommon for students to bypass internships because they’re recruited directly for a job. After completing her first year in the Microelectronics Technology Program, Jessica Iles found work at Intel Corp’s Aloha campus.
“I took the opportunity of starting the job a year before I graduated, and it offered me a great head start for my career, as well as higher motivation to finish my degree,” said Iles, who is the first in her family to attend college. “I was able to be one of the very first people in my program to be hired before earning my degree.”

I would not recommend working for any manufacturing company for longer than it takes to get a job with better pay, better conditions and better focus on true leadership. I worked at a local manufacturing company for 15 years. The standard level of pay is generally 30% less than in other industries. Management is not leadership focused. People who are on the production room floor(s) are not treated with respect. The standard of behavior for management is very low. Leadership is all but nonexistent. Go do the manufacturing job; but think of it as an entry-level stop gap while you’re looking for something better. Here’s a hint: you won’t have to look very far for very long.